
Knee stretch marks are more common on skinny and slim jeans because of the way the fabric stretches when worn and the stress that comes from bending your knees. When it comes to jeans with a looser fit around the knees, the effect will be minimal to nonexistent.
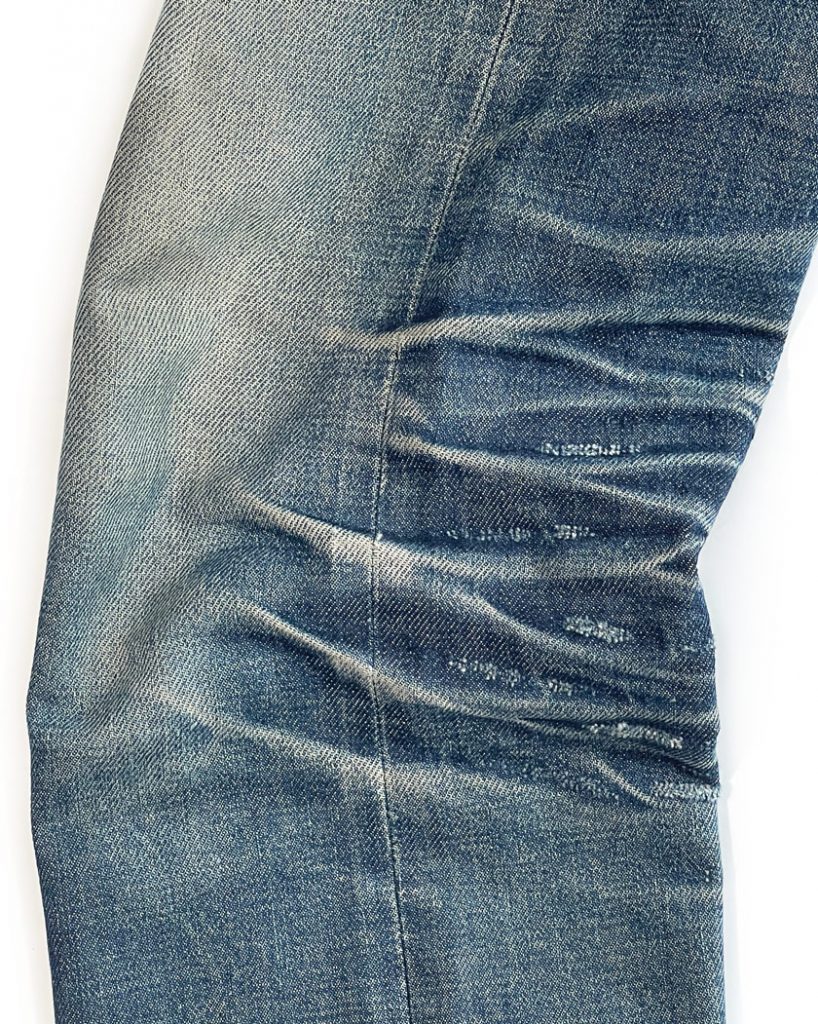
The effects of stretching start from the center back of the knees as honeycombs that extend over the seams to the front. Just beyond the seams, the stretch marks quickly lose their height, depth, and color as they fade into the knees.