If you’ve ever typed how to take in the waist of jeans into Google, you’ve probably seen a lot of DIY tricks—some good, some pretty questionable. But here’s the thing: there’s a world of difference between a quick fix at home and
Read More →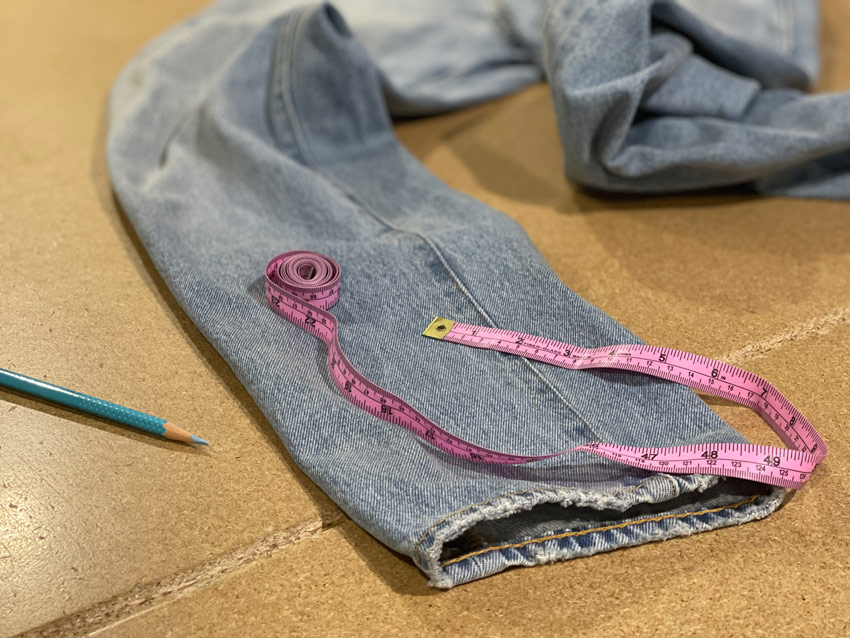
The goal of this tutorial video is to walk you through the complex process of determining the inseam of twisted-leg jeans. In contrast to measuring the inseam on a pair of typical jeans or pants, dealing with twisted legs adds an additional level of complication. When the legs of the jeans wrap around to the opposite side, the dilemma of whether to follow the inseam line arises.
The short answer is no. The key is to follow the natural shape of the jeans as though there were no twist. In this video, we show you step-by-step how to do this.
In addition, we explore some of the frequent mistakes that tailors and clients requesting hemming alterations make while shortening the inseam. This guide will educate you on why using a general request like “take off 2 inches” while asking for a hemming service may not be the best choice. Similar to this, we show how this approach can result in mistakes when shortening jeans for tailors who often align the hems of jeans before simply cutting them. Have a look at our video to enhance your understanding and skills with denim alterations.
You might be interested in
If you’ve ever typed how to take in the waist of jeans into Google, you’ve probably seen a lot of
The first brand in our new lineup was TCB Jeans, a company out of Kojima, Japan that builds its reputation
The leg opening measurement is a critical factor in how your jeans fit over your shoes and shape your overall
Washing raw denim has long been a topic of debate. Some purists believe in waiting as long as possible, while
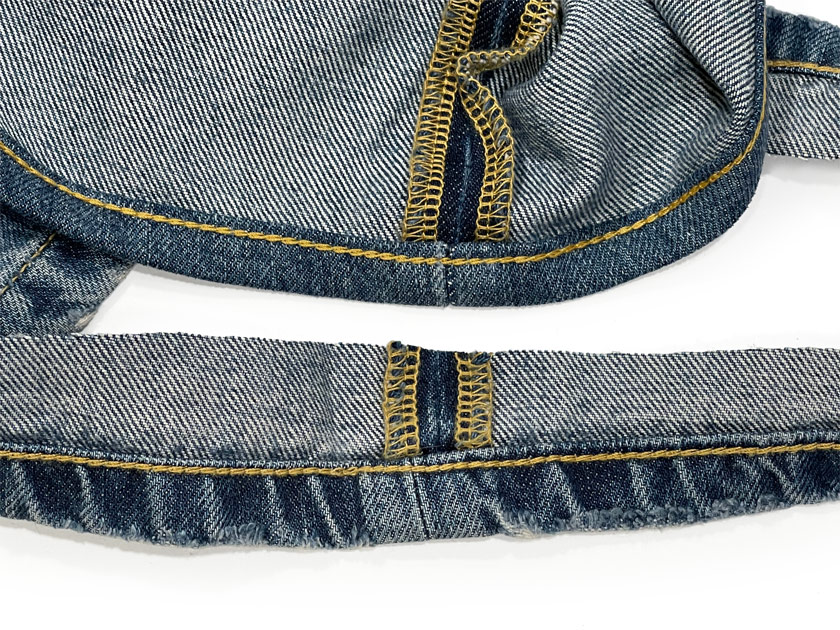
In this brief social media video, we show how to hem jeans professionally, just like it’s actually done at denim factories. In our video, there is no need for work-around-sewing-techniques, which leave bulky seamlines over the hem or ragged fabric on the reverse side, which prevents cuffing or rolling the hem. We love denim at Williamsburg Garment Company and hemming jeans the right way is important to us.
Even the heaviest denim is no problem for our beast of a sewing machine, a customized Union Special 56300 that bores through multiple layers of folds and seams. Here, denim designer Maurice Malone demonstrates chain stitch hemming a pair of jeans in our Instagram and TikTok video. Make sure to stay tuned and follow us for more.
You might be interested in
If you’ve ever typed how to take in the waist of jeans into Google, you’ve probably seen a lot of
The leg opening measurement is a critical factor in how your jeans fit over your shoes and shape your overall
Washing raw denim has long been a topic of debate. Some purists believe in waiting as long as possible, while
When it comes to buying jeans—especially online—getting the right inseam measurement is crucial for a proper fit. Whether you’re checking

“Can you tailor denim jackets?” is a frequently asked question at Williamsburg Garment Company. Our answer, as with all denim products, is, of course, yes, but jackets and shirts are more complicated. They have armholes and shoulder widths that correspond to the width of the body. When you narrow the body width evenly, the armhole shrinks and the armpit curve is negatively affected. At the same time, the shoulder width remains constant, resulting in wide shoulders compared to the body width. The only way to avoid this is to remove the sleeves and, if possible, draft new armholes and sleeve shapes. Otherwise, you can leave the armhole alone and narrow the body unevenly from the chest/armholes down.
Nothing about modifying denim jackets is simple or easy. The body width is linked to the armhole and shoulders, whereas the sleeve length is linked to the button placket length and/or the armhole.
Can you tailor denim jackets on a home sewing machine?
When it comes to DIY denim jacket alterations, the short answer is that you can do it, but it is not recommended. If you’ve done any research on the subject, you’ve probably discovered that all of the videos and advice you’ve seen have had poor results on cheaply made garments.
Flat-felled seams on the sides, shoulders, and sleeves distinguish traditional jean jackets. This design eliminates the option of doing high-quality alterations on home sewing machines, at your local dry cleaners, or at the best, most reputable tailoring shops. Most denim alterations specialists lack the factory equipment (a Feed-off-the-Arm 3-Needle or Double Chainstitch Industrial Sewing Machine) to duplicate the double-needle flat-felled seam with chain stitching and must come up with an improvised method to sew them.
Most denim jackets and jeans are produced with fabric that is too thick for home machines. To tailor denim on a home sewing machine, you would need to avoid thick seams or deal with really thin, lightweight denim fabrics.
Thread size is also an issue with DIY and most tailoring shops. Denim is typically sewn with thicker thread sizes than most other garments, which contributes to its distinctively sturdy appearance. Home machines are not designed to handle the needle sizes required for thick threads. They also lack the ability to puncture through layers of denim using wide-diameter needles with large eye holes. Thin thread sizes and short stitch lengths are two of the reasons why denim does not look like denim when it is not sewn with the proper threads.
How altering a jean jacket professionally is done
The owner of this heavyweight Oni Denim jacket adored it, however, he had a small frame and required the chest and arms reduced. Here are the steps we used to customize his denim jacket:
1. Chain-stitched flat-felled seams close the sides and sleeves of traditional jean jackets. Because the band at the bottom is chain stitched to the jacket, our first step was to remove the chain stitching connecting the waistband to the body, just enough to remove excess fabric and resew the seams closed.
2. Following that, we split the waistband and removed the chain stitching that held the flat-felled seams together from the waistband to about 6 inches from the cuff seam. After narrowing the excess fabric around the bicep, just past the elbow, we could neatly flow into the sleeve.
3. We press flat the flat-felled seam folds in order to draw the new shape from the waistband up to the armpit and then fade out the shape before reaching the cuff.
4. The seams were then closed (as indicated in the image below) by stitching fresh double-needle chain-stitched flat-felled seams using the same thread size and color as the original. If you look closely at the yellow chain stitching, you can see where the new sewing blends in with the old.
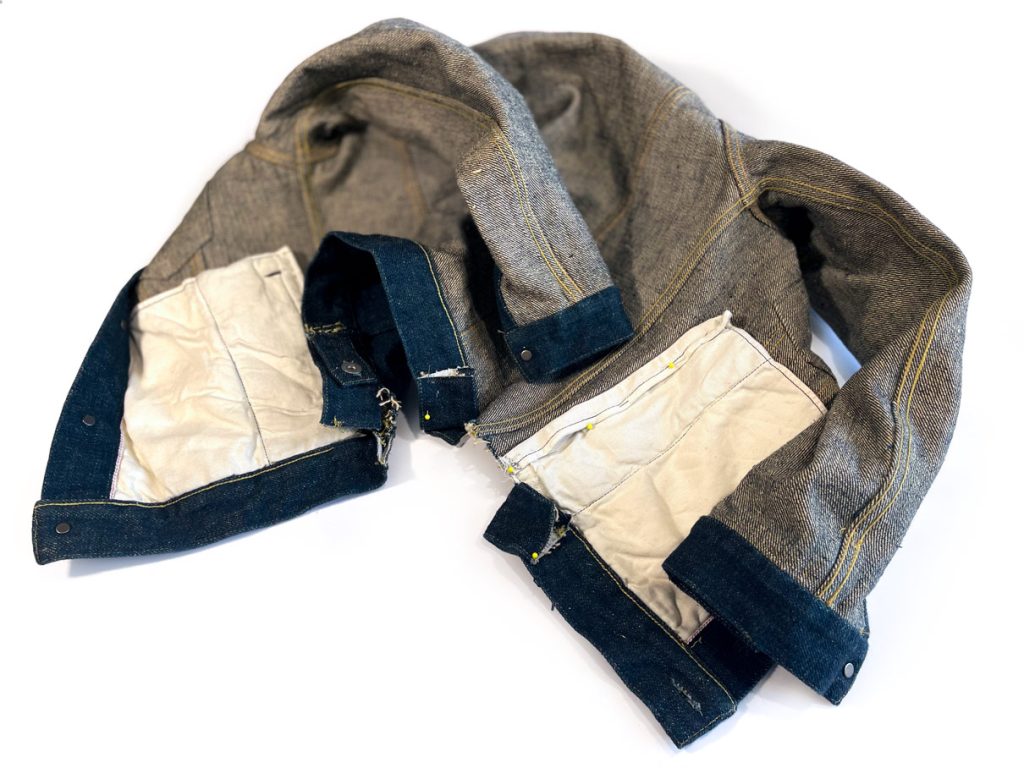
6. After cutting away the extra fabric of the bottom band, we rejoined and resewed it to the body with single-needle chain stitching.
7. Finally, the band tabs along the side seams were reattached. Again, if you look very closely, a seamline where the waistband was split and resewn can be seen near the two yellow stitch lines that attach the tabs. Take note of the new chain stitching that joins the old one below the pocket bag.
Williamsburg Garment Company’s objective is to make alterations to improve fit while retaining the original style and construction. This entails matching thread colors and sizes and stitching seams back the same as the original factory sewing.
You might be interested in
If you’ve ever typed how to take in the waist of jeans into Google, you’ve probably seen a lot of
The first brand in our new lineup was TCB Jeans, a company out of Kojima, Japan that builds its reputation
The leg opening measurement is a critical factor in how your jeans fit over your shoes and shape your overall
Washing raw denim has long been a topic of debate. Some purists believe in waiting as long as possible, while
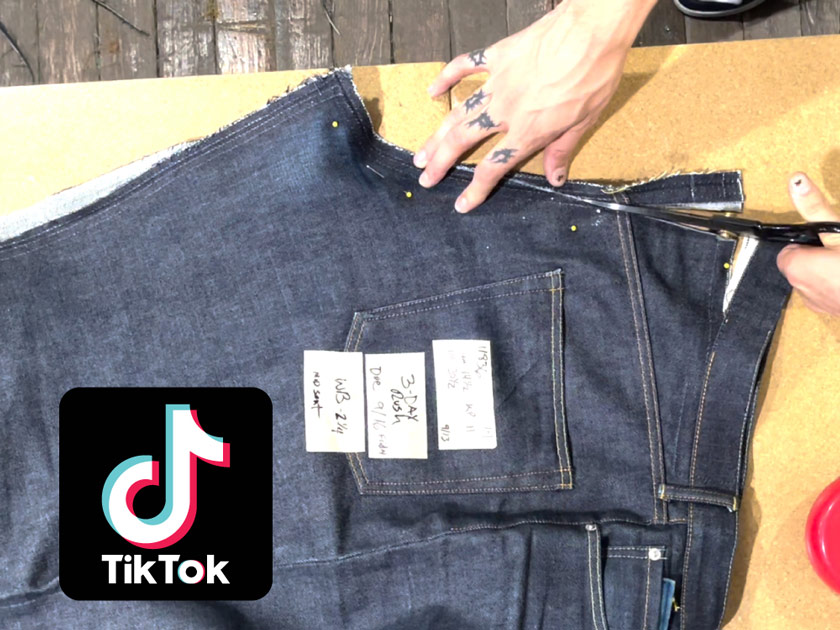
Do you want to know what sets us apart from the competition when it comes to denim alterations? In our latest TikTok video, you can see how we professionally taper the legs of a pair of jeans while also taking in the waist to make them fit just right.
@williamsburggar Denim heaven. The art of taking in the waist with tapering alterations on jeans. We perfect your fit. #denimyourway #denimhead #denimtailor #taperingjeans #jeanswaist #jeanswaistgap #selvedgedenim ♬ MAMBO OVER THE MOUNTAIN – Rick Hirsch
Make sure to follow us on TikTok to see more informative and entertaining videos. @williamsburggar
You might be interested in
If you’ve ever typed how to take in the waist of jeans into Google, you’ve probably seen a lot of
The first brand in our new lineup was TCB Jeans, a company out of Kojima, Japan that builds its reputation
The leg opening measurement is a critical factor in how your jeans fit over your shoes and shape your overall
Washing raw denim has long been a topic of debate. Some purists believe in waiting as long as possible, while
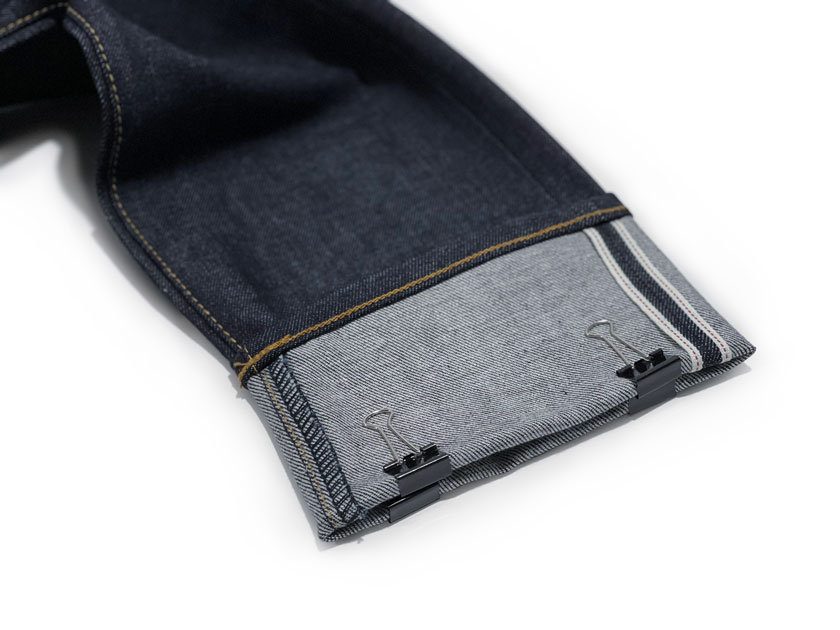
Here’s what to do if you want to send your jeans or pants to a tailor for hemming service but don’t have a measuring tape. Because everyone has their own personal style, we won’t get into whether or not your pants should have a break, no-break, or hang just above your shoes. We will give you a few good tips on how to mark your desired inseam length.
- Put on your pants and approach a mirror wearing the shoe style you prefer with your pants.
- Cuff or roll the legs of your pants to the desired inseam length.
- Select the best-fitting leg, then bend down and secure it with a pin or clip at the folded edge.
- Uncuff or unroll the second leg so there is no confusion about which leg to use as the standard.
- Ship or hand-deliver the pants to your tailoring service and instruct them to follow the marked leg.
Because most people never mark both legs exactly the same, it is best to mark one leg. If the tailor needs to contact you to determine which size of the two legs is best, the tailoring process may be slowed.
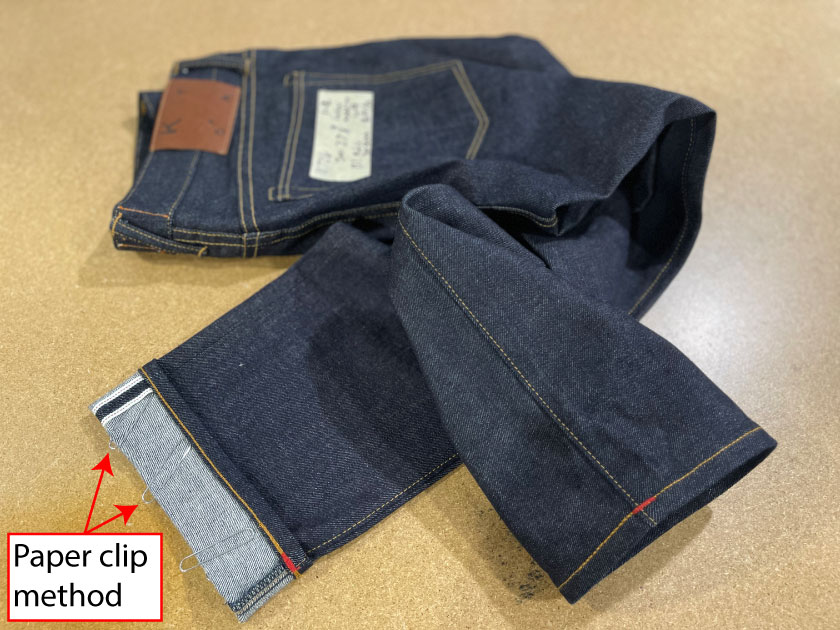
If you don’t have a clip or pin, use an iron to press the cuff into place for a secure hold during the shipping or drop-off process. You can also mark the location with washable chalk or tape.
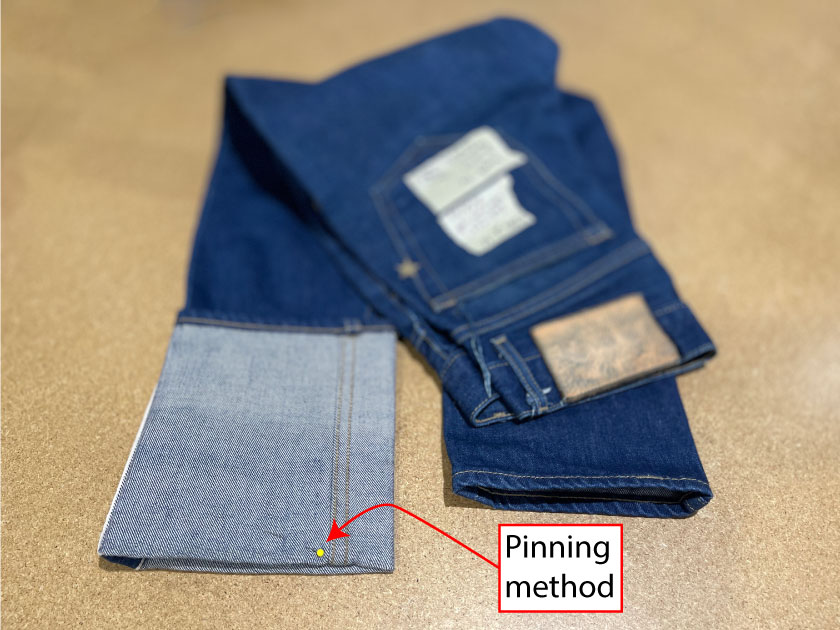
You might be interested in
If you’ve ever typed how to take in the waist of jeans into Google, you’ve probably seen a lot of
The first brand in our new lineup was TCB Jeans, a company out of Kojima, Japan that builds its reputation
The leg opening measurement is a critical factor in how your jeans fit over your shoes and shape your overall
Washing raw denim has long been a topic of debate. Some purists believe in waiting as long as possible, while
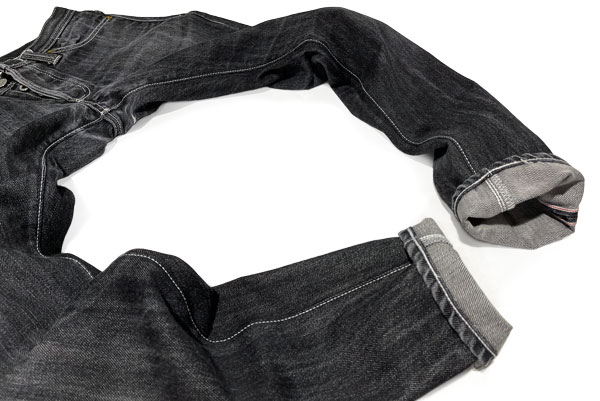
It seems needless to say, selvedge jeans should always be tapered from the inseam. However, some people still take jeans to local tailors or dry cleaners, who are not equipped with proper denim sewing machines and expect them to properly taper their jeans.
Tapering jeans with double-needle chain stitched flat-felled seams
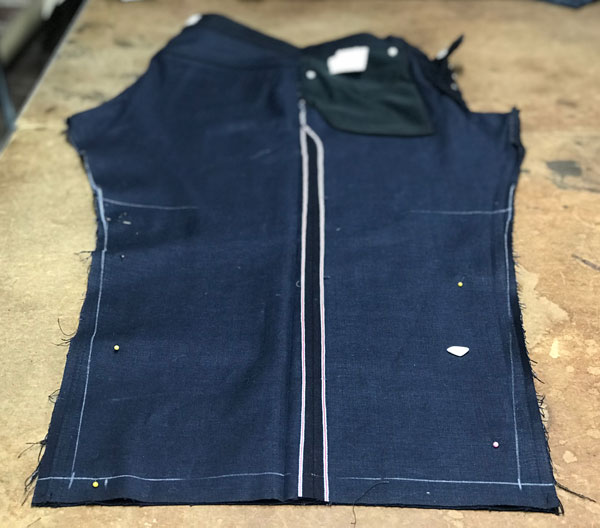
This photo shows an example of tapering from the inseam in-process. These jeans were sewn with a double-needle chain stitched flat-felled (lap seam), so it has to be taken apart at the inseam. With the selvedge outseam shown at the center, the inseam is then trimmed to slim the leg down. Slimming is done from the hem, up to just above the knee, and eases out at the thigh.
A tailor without a feed-off-the-arm chain stitch sewing machine will never properly taper a pair of jeans with lap seam construction. Instead, they may use makeshift single needle sewing from the hem to the knee area. Leaving the area around the crotch and thigh with the original sewing, connecting the new sewing into the original.
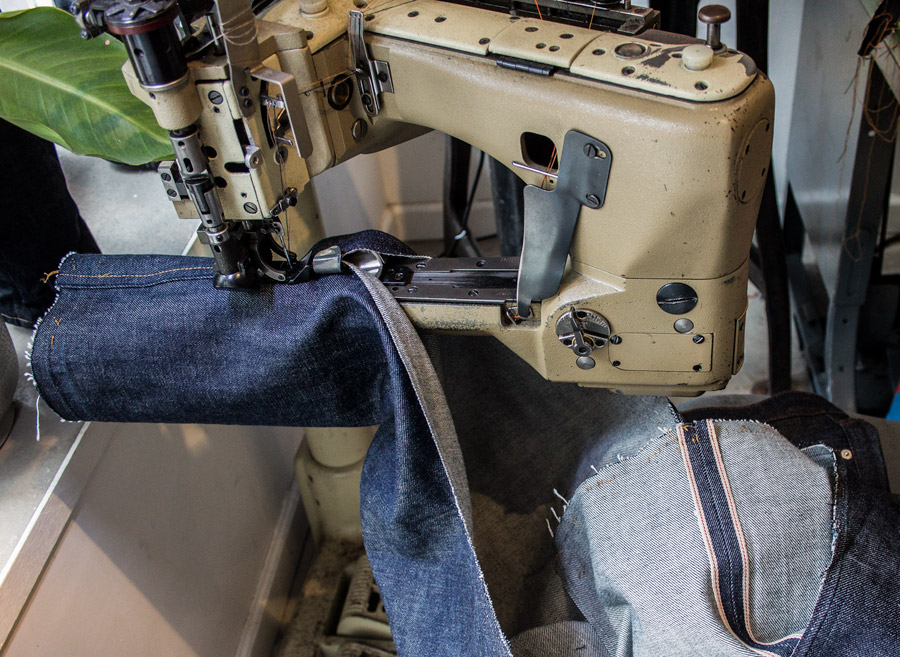
For more detail on how we taper jeans constructed with a lap seam, watch our popular Youtube video.
How to taper jeans professionally
How to taper jeans with a single-needle overlocked inseam
Not all jeans have two needle chain stitch lap seam construction. Some have a single-needle topstitched inseam with overlock construction. We tapered the below Levi’s jeans, slimming the legs down and the excess fabric cut from them can be seen underneath.

Most tailors can handle overlocked jeans much easier than lap seams. Overlock sergers are machines commonly used by tailors. However, similar to how traditional tailors may handle lap seam sewing, they will likely remove the original topstitching to just above where the tapering will end. Then use the serger to sew the new leg shape. Finally, to reach high on the leg, so new topstitching can join with the original, the outseams are opened and subsequently closed after topstitching the inseam.
Process for tapering jeans with overlocked inseams as also seen in our TikTok video:
- Cut the inseam to the requested inseam length, plus 3/4″ to 1″ (depending on the hem height)
- Remove the single stitch on the inseam
- Press the inseam flat & draft the taper lines on each leg
- Trim & sew the new leg shape with a serger sewing machine
- Press the inseam to remove slack
- Sew a new single-needle chain stitch on the top of the inseam
- Chain stitch the hem
@williamsburggar This is how we taper jeans with a single-needle top stitched inseam. #selvedgedenim #samuraijeans #denimtailor
♬ original sound – Williamsburg Garment Co.
Depending on the details of the tapering, we first remove the entire original topstitching in order to sew a new unbroken/unjoined line. It doesn’t matter if the taper is to the knee, above the knee, or high into the thigh.
We taper jeans high into the thighs only when we get requests to make the thigh smaller. We always advise, that very little can be done at the thigh. Explaining, that the width of the thigh is in connection to the pattern’s shape. The seat, rise, and curve in the crotch (which affects movement) are all connected. Decreasing the thigh means the curve must be shortened and straightened, which will restrict movement. Taking from the curve also lowers the rise.
In other words, the best we suggest is easing the taper from the knee, high into the thigh, clipping a bit of the curve, thus reducing the thigh to a maximum close to 1/2 inch. We don’t feel comfortable taking much more.
Looking closely, the original overlock stitching can be seen in white thread and the new sewing in tan color. These jeans were tapered high, so we went completely around the crotch.
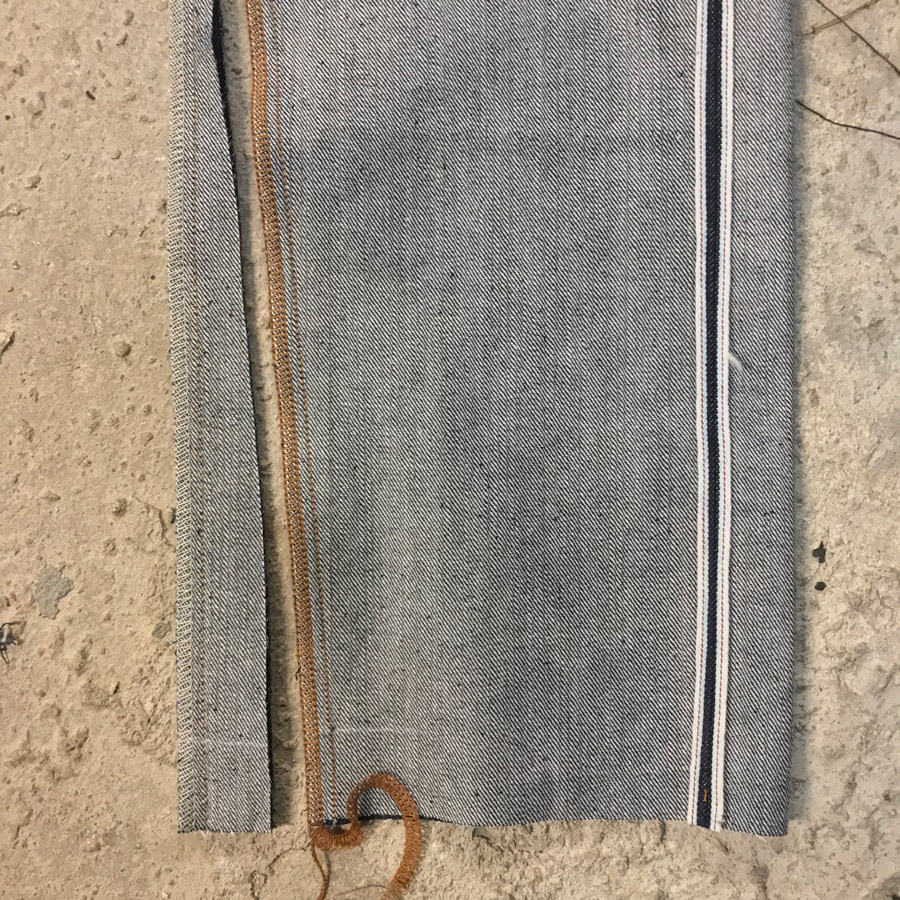

As demonstrated in the TikTok video below, one of the biggest things that separate our work from tailors and denim specialists is our use of the Union Special feed-of-the-arm chain stitch machine. On single-needle overlock constructed jeans, it allows us to completely topstitch the inseam from hem to hem without opening the outseams.
@williamsburggar Williamsburg Garment Company quickly explains how to professionally taper jeans. Setting us apart from common and amateur tailors, we take the pants apart, redraft the shape, then sew them back together following the original factory’s construction. #denimhead #selvedgedenim #denimtailor #taperingjeans
♬ original sound – Williamsburg Garment Co.
The Union Special is advantageous with selvedge jeans because you don’t want to disturb the outseams. Tailors who have to rely on tapering at the outseams will destroy the beauty of the selvedge jeans. The photo below is an example of what can happen when you give your jeans to a local tailor who doesn’t specialize in or understand denim. Luckily, he later did some research, found us and we saved his jeans.
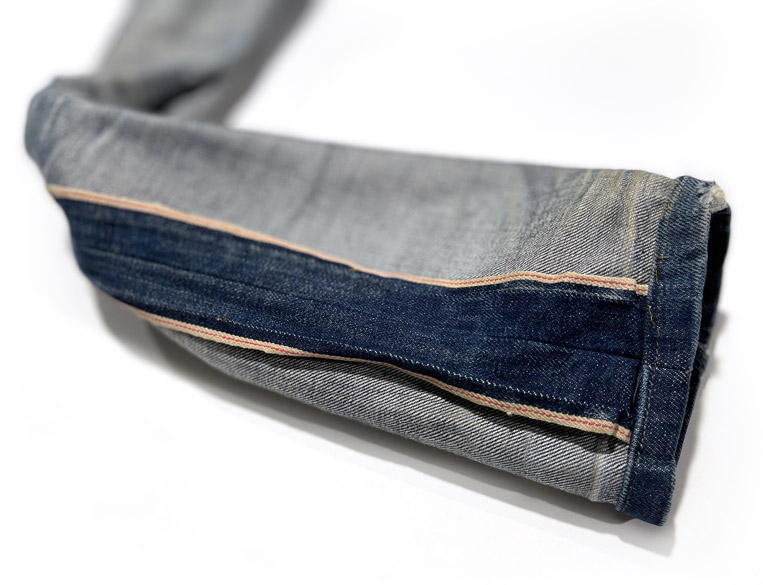
You might be interested in
If you’ve ever typed how to take in the waist of jeans into Google, you’ve probably seen a lot of
The first brand in our new lineup was TCB Jeans, a company out of Kojima, Japan that builds its reputation
The leg opening measurement is a critical factor in how your jeans fit over your shoes and shape your overall
Washing raw denim has long been a topic of debate. Some purists believe in waiting as long as possible, while